RMIT University: Aussie tech helps make bio-oils for greener industrial applications
- Global Research Partnerships
- Apr 16
- 2 min read
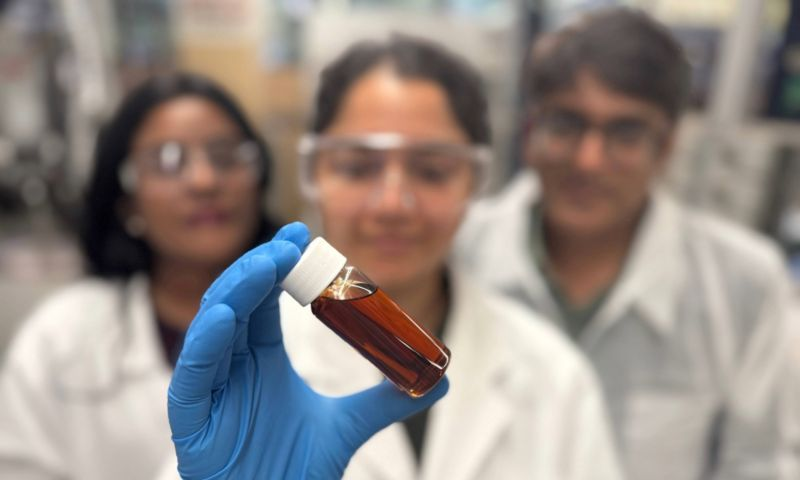
Australian technology developed at RMIT University could enable more sustainable and cheaper production of bio-oils to replace petroleum-based products in electronic, construction and automotive applications.
The technology, known as PYROCOTM, uses high temperatures without oxygen to convert treated sewage (biosolids) into a carbon-rich product called biochar, which can act as a catalyst to produce phenol-rich bio-oil.
PYROCOTM has been developed by RMIT in collaboration with South East Water, Intelligent Water Networks and other water authorities over several years and is now being applied to several exciting circular economy applications.
The RMIT team's latest research in collaboration with the Indian Institute of Petroleum, published in Renewable Energy, highlights that biochar derived from biosolids can effectively replace the expensive catalysts currently used to extract oil from biomass such as Willow Peppermint, a plant native to Australia.
This discovery shows that biochar from biosolids, produced using advanced pyrolysis technology such as PYROCOTM, offers a sustainable way to reduce carbon dioxide emissions by replacing high-emission products.
The use of biochar made from biosolids as a catalyst could underpin a sustainable supply chain for bio-oils rich in phenol that are essential for making valuable chemicals such as resins, lubricants and additives used in various industries.
The researchers produced bio-oil with high levels of phenolics (69%) and hydrocarbons (14%) during their experiments, showing their biochar to be an effective catalyst.
Scaling up
RMIT’s Professor Kalpit Shah, Deputy Director (Research) of the ARC Training Centre for the Transformation of Australia’s Biosolids Resource, said PYROCOTM was close to commercial-ready scale.
RMIT and partners Aqua Metro, South East Water and its commercial arm Iota have secured $3 million from the Australian Government to build a commercial-scale demonstration plant (Mark-3) at one of the water recycling plants at South East Water next year.
“Our upcoming project aligns with the Global Waste Management Policy and Australia’s National Waste Policy Action Plan. Our goal is to prevent PFAS-contaminated biosolids from being disposed of in landfill by converting them into PFAS-free biochar, for its diverse applications,” Shah said.